

Note: you can also see our top 5 MIG wire picks here. There’s nothing worse than getting the wrong size and having a useless reel you worked hard to buy sitting around. The bigger a spool you buy, generally the less it will cost if you compare the length of wire you get.ĭon’t go buying a reel that won’t fit your welder. The capability of your welder’s spindle and the amount of welding you’ll be doing will determine the size of reel you buy. You don’t want a tidy stainless project ruined by rusty welds because you bought the wrong wire for it. It makes a significant difference in weld quality, especially if you’re welding stainless steel. Make sure you’re buying steel wire for steel welding, and stainless steel wire for stainless steel welding. Know what the wire you’re buying will be used for before you purchase it, to ensure it’s exactly what you’re after. Some are only good for welding clean steel. Some of the best flux-cored wires are better for welding dirt and coatings than others. What and where you’ll be welding also determines which wire is better. Be aware of the specific wire’s specs before you determine this, as these differ among wire types. The thinner the plate you’re welding is, the smaller-sized a wire you want as well. The lower your amperage is, the smaller a diameter your wire should be. However, the amperage your welder runs at and the plate you’re welding will require specific wire sizes. These can usually be adjusted or changed easily. The best flux core wire size will be determined by the size your welder can accommodate, including feed wheels and nozzle tips. Make sure you don’t get the wires confused and end up with a flux-cored wire that doesn’t shield your weld.
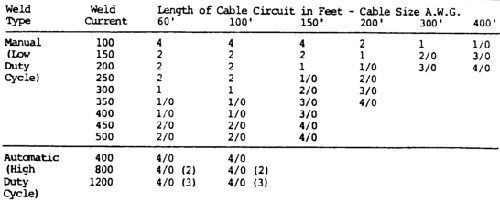
Some require a shielding gas to be used alongside them to keep air and dirt from ruining your weld. Most wires are made for gasless operations, like all six types we reviewed above. When buying flux-cored wire, it’s essential to know what type you’re buying.
#FLUX CORE WIRE SIZE CHART HOW TO#
Flux-cored wires are best on mill scale, but with their lower efficiencies (loss of material in the form of slag) will result in lower deposition rates.Īs with many things in welding applications there are exceptions, but in general this is what our observations in the field support.Buyer’s Guide: How to Choose the Best Flux Core Wires Solid wire will probably require you to slow down to insure there are no weld discontinuities caused by the mill scale. Its ability to deal with mill scale and provide smoothness at the toes allows metal-cored wires to shine in this application.
